31OCT 2014
© Lawrence lek “I remember a lot of students’ work, and mine especially, could be very extravagant with materials because being in school you have the luxury of many resources… One thing I found difficult just after leaving the academic world was actually fabricating prototypes.”Without the ability to move freely between digital modeling and CNC milling, not to mention the wealth of other equipment available to him at AA, Lek decided to simplify his entire approach. “I use materials in an economical way out of necessity rather than an aesthetic idea,” Lek said. “I try to make the most effective shape from limited materials.
© Lawrence lek” Instead of seeing this as a burden, Lek commented, “Thrift is the opportunity to create something completely unexpected from a very simple material technique, making the most of whatever opportunities or materials you immediately have.”
Lek decided to make a pavilion because, among other reasons, “it’s like an extra small, deluxe version of an architect’s work.” He also wanted to see whether he could apply his experiments with bending plywood to create strong, modular, free standing, three dimensional forms that could be transported and assembled with ease, and then disassembled and used for something else. He began by experimenting with symmetrical shapes found in nature and cut small, Rorschach-like patterns out of paper, combining them in a variety of formations.
© Lawrence lek He then made models from thin pieces of plywood, which he soaked and shaped into place. After the wood dries and the ties binding it into place are removed, the wood retains its shape without compromising the integrity of the materials. “I’m using plywood, which is lightweight but just thick enough that when it forms a shell it can be quite strong.
© Lawrence lek Also I want it to be light so you can transport it just by carrying it in pieces. That’s more like a tent, whereas most pavilions are made with really thick and heavy components that need a crane to be put into place.”Once Lek developed a stable shape he tested it out with larger pieces cut from full size 4-by-8-foot plywood sheets by a CNC miller. He used the larger shapes to make furniture as well as modular units that he used to create the “Unlimited Edition” pavilion.
© Lawrence lek He built a water tank slightly larger than the 4-by-8-foot sheets so he could soak them in his studio. Wrangling them into shape by himself was markedly more difficult than shaping his original palm-size models, but Lek was able to make the six pieces he needed to build the pavilion, which he secured with zip ties.Though Lek’s acceptance into the Designers in Residence program afforded him the means to develop this fabrication process, he’s still experimenting with all the possible applications. Potentially, Lek can patent his design and either sell the basic plans or manufacture and flat pack the pre-soaked plywood forms themselves.
© Lawrence lek More importantly, his experiments show how large, sophisticated structures can be made from the most basic materials and processes. Wasteful fabrication methods and costly materials are not only unnecessary, they act as a barrier between a person interacting with the raw functionality of the space. “Most design products are designed to be stand alone objects,” said Lek, “but it’s when I join them together that they form another structure as well. That brings me back to my initial interest with design, playing with forms that by themselves don’t really do anything, but it’s when you join them together they suggest a function.
© Lawrence lek”.
© Lawrence lek
© Lawrence lek
© Lawrence lek
© Lawrence lek
© Lawrence lek
© Lawrence lek
© Lawrence lek
Lawrence lek / UNLIMITED EDITION
Posted in Architecture - Installation by * FORMAKERS
One of the four chosen proposals came from Lawrence Lek, an architect and sculptor who worked with Ken Yeang in Malaysia and Foster + Partners in London before founding his eponymous studio in 2011. For his project, “Unlimited Edition,” he reflected on how he has approached fabricating prototypes since completing his studies at the Architectural Association (AA) in 2008.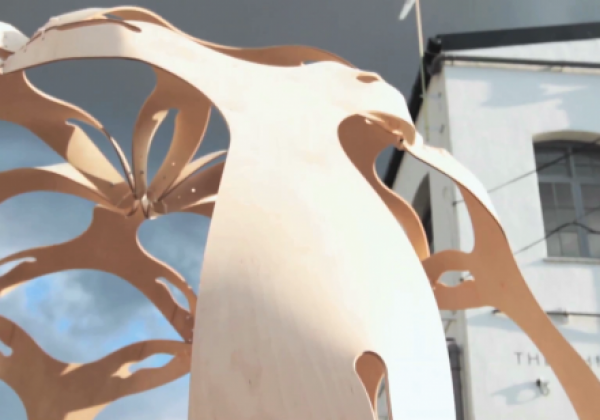
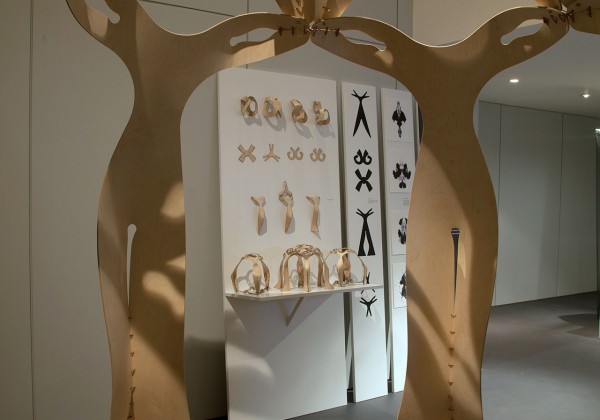
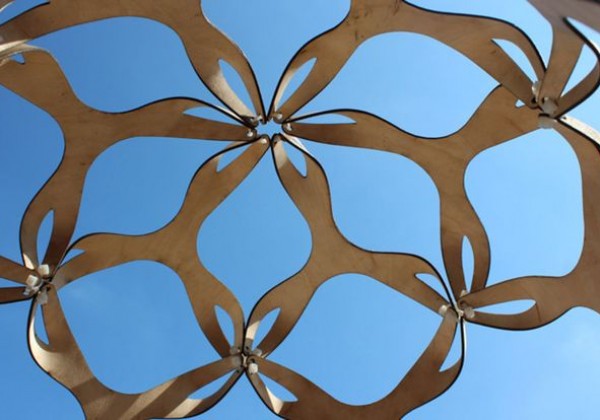
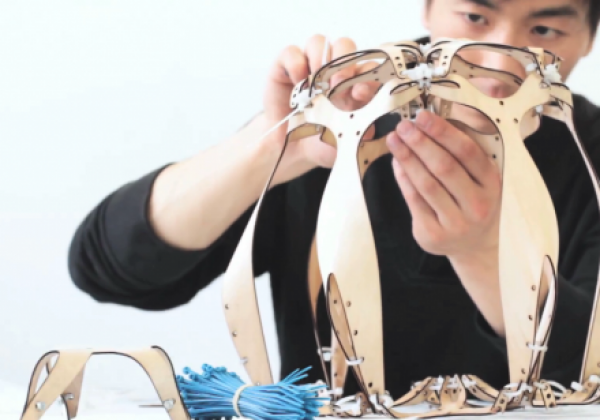
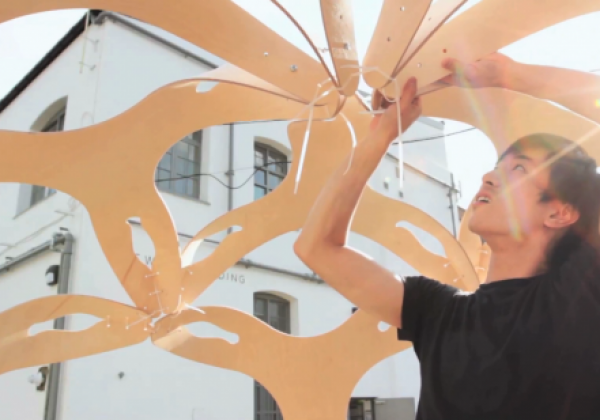
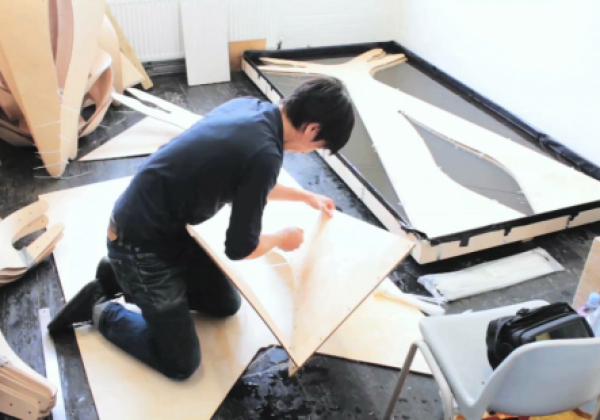
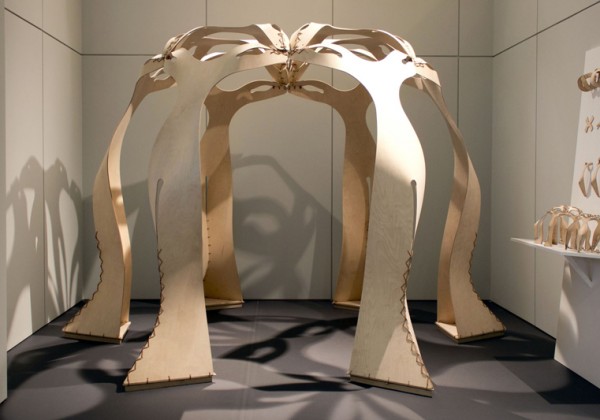
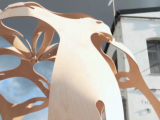
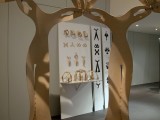
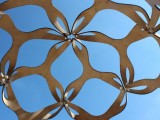
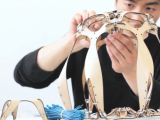
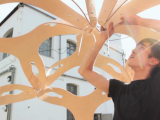
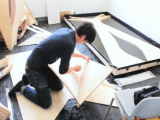
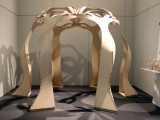
Comments
No comments
Sign in »