09JAN 2014
© Hayato Wakabayashi Buckminster Fuller already pointed out that in experimentation there are not failures, but only unexpected results. For Obuchi this project persuasively has surpassed the threshold of being solely a scaled‑up version of a desktop model to the exclusive quality of small scale architecture.
© Hayato Wakabayashi If earlier studies of the Minimum Surface Pavilion (2011) and Circle Pack Pavilion (featured partly in Domusweb 19 of November, 2012) speculated on the possibility for exhibiting structural studies in rather sculptural mode, then 99 Failures Pavilion reveals highly immersive structural, material and spatially perceptual experiences.The DNA of the pavilion is the Lab’s investigations of structural and material behaviours in tensegrity models.
© Hayato Wakabayashi Tensile and self‑stressed structure studies can be dated back already to the 1940’s, originating from explorations on balancing tension and compression forces in sculptural objects. In the 1960’s Buckminster Fuller coined the concept of tensegrity as synergetic explorations in structure and geometrical forms. Within the context of digital advancements in the 21st Century, which radically expanded the investigations of topological surfaces and structures, the tensegrity studies of Digital Fabrication Lab are aimed at generating prototypical geometries to reconcile with the contemporary issue of limited resources and materials.
© Hayato Wakabayashi In this sense, the pavilion has also been a conceptual and practical vehicle for generating series of challenging computational design questions instead of finding straight‑forward engineering solutions to some structural or material related problems. Obuchi points out that studio projects can be limited in their level of complexity and especially in relation to the parameters and constraints of what computational should or could be dealing with in real construction.
© Hayato Wakabayashi This kind of next-level engineering and architectural quality has been achieved through unprecedented collaboration between the Digital Fabrication Lab, structural engineers and construction related industries. One of the main collaborators, Obayashi Corporation, was invited to help choosing one of the studio tensegrity models for development into the real construction and further structural explorations.
© Hayato Wakabayashi Digital Fabrication Lab’s course assistant Toshiktasu Kiuchi remarks that the final choice was related to the potential of the geometric form to be controlled and calibrated along the process of construction. Japan is the country with the largest number of robotic arms being used in the industrial assembly lines, supported by the highly advanced studies in technologies, engineering and robotics. Beyond developing prototype architecture and material studies, another ambition of the Digital Fabrication Lab is to democratize the exclusive industrial use of robotics for the purposes of fabricating architectural components.
© Hayato Wakabayashi As Yusuke Obuchi explains, at the moment architects are able to give very precise instructions of geometries of their designs, but construction to a great extent still relies on the traditional means of building. While computational design came later in the Japanese architectural scene compared to other countries, it would be adventurous to foresee in detail which new directions it will undergo in the coming years.
© We might be already witnessing a very particular reconciliation between architects, building processes, techniques and knowledge. It is for sure that those who pursue these paths for innovation will continue risking and tasting the sweet flavour of failures.
.
© Hayato Wakabayashi
© Hayato Wakabayashi
© Hayato Wakabayashi
© Hayato Wakabayashi
© Hayato Wakabayashi
© Hayato Wakabayashi
© Hayato Wakabayashi
©
on Vimeo - ©
99 Failures Pavilion / University of Tokyo, Digital Fabrication Lab
Posted in Events_Interviews - Events_Interviews by * FORMAKERS
Thus 99 Failures is the name of the third pavilion undertaken by Digital Fabrication Laboratory at The University of Tokyo in Japan, founded by initiative of Kengo Kuma and Yusuke Obuchi. For the later to fail is not necessarily something catastrophically wrong, and rather opens the possibility for new explorations.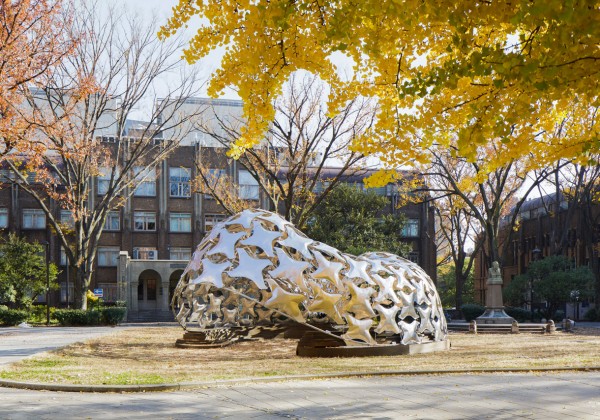
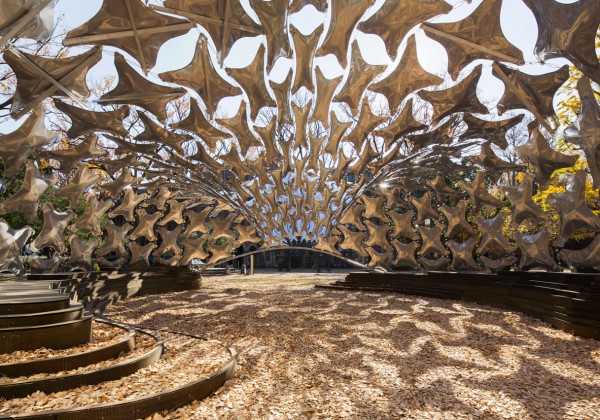
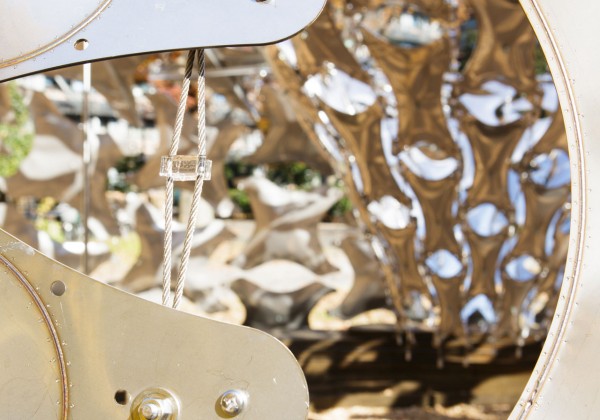
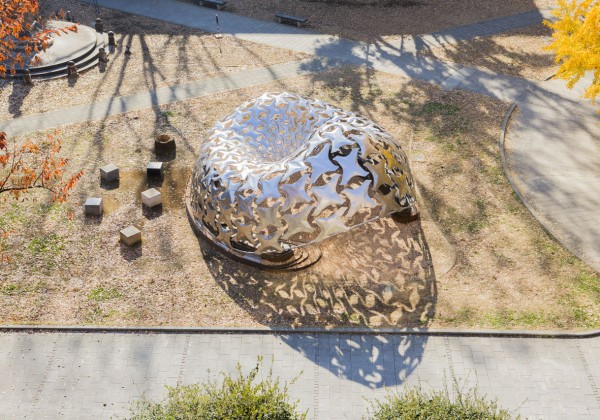
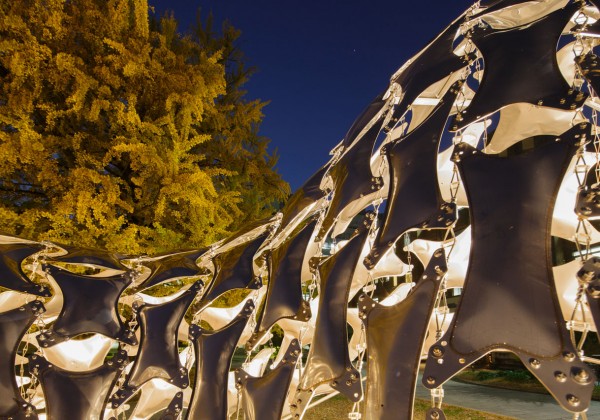
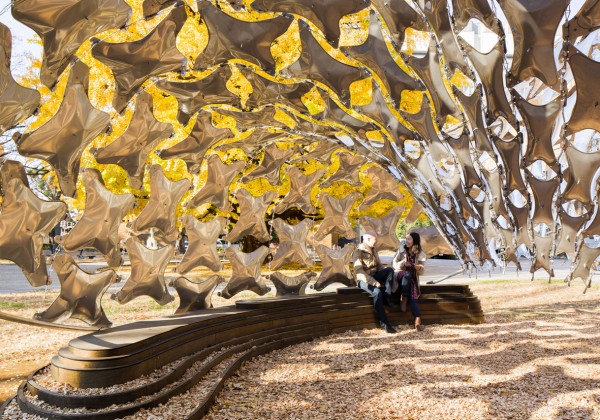
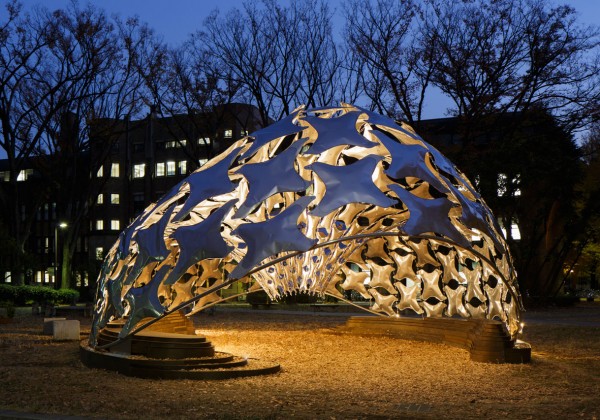
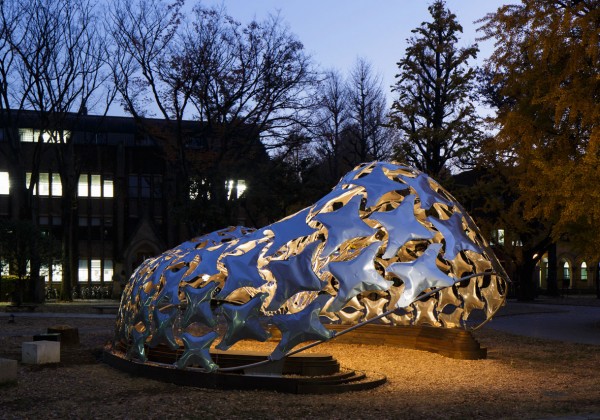
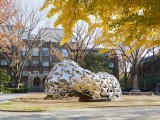
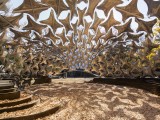
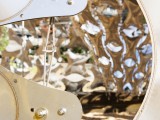
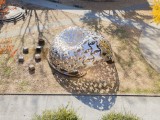
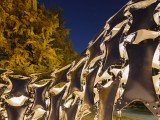
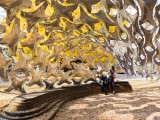
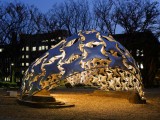

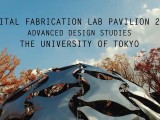
Comments
No comments
Sign in »